ATMAGP 50PP
CCD REGISTERING SCREEN PRINTER with 3/4 automatic vacuum shuttle unloading.
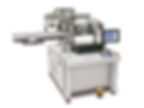
FOR SCREEN PRINTING ON GLASS PANEL
This model is specialized in automatic centered registering for high precision printing on touch panel display without fiducial mark, effectively solving tolerance of glass outline to obtain precise centered printing.

Max Print Area: 300mm x 400mm (11¾" x 15¾")
Substrate Thickness: 0.3 - 2.0 mm (0.01" - ⅛")
ATMAGP 50PP CCD Centered Registering Screen Printer with 3/4 automatic vacuum shuttle unloading. Substrate is loaded manually.
GENERAL STRUCTURE
• Smooth Movement: Substrate is moved by sliding table and offloaded by vacuum pad.
• Energy Saving: Efficient electro-dynamic design with extremely low air exhaustion results in significant energy savings.
• The control system for compressed air supply is an oil free FRL unit to prevent oil mist pollution, particularly applicable in clean room environments.
SCREEN UP/DOWN
• Accurate Positioning: Screen up/down structure is driven by German motor on high-lead ball screw rod and encoder with digital control. Movement is fast, smooth, and silent, with positioning accuracy ±0.05mm.
• Horizontal head lift keeps screen parallel with printing table for even ink flow.
SLIDING TABLE
• Stable & Precise: Shuttle table is driven by servomotor with timing belt for stable movement and highly accurate positioning.
• Hydraulic Buffer: Hydraulic buffer and electromagnet ensures shuttle table positioning accuracy within 5µm.
• Vacuum Suction: Silent vacuum system holds glass substrate during sliding table movement and printing.
• Efficient Design: Eight pop-up pins facilitate manual loading and prevent scratching of glass substrate while loading.
REGISTRATION PLATFORM
• Table Surface: 12mm thick aluminum alloy with hard anodizing treatment to prevent scratches.
• Optional Slotted Table: Table can be slotted for zero off-contact printing, customized for glass substrate size for quick positioning.
• Fast Registration: Exclusive software for automatic registration controls 3 servomotors to rotate printing table u/v/w axis for fast and accurate displacement and registration.
• CCD Camera Registration: Optical alignment system can automatically judge and control displacement of printing table. High precision mechanism and fully automatic printing table alignment system can achieve alignment repeatability accuracy of ±5µm. Alignment speed < 1.5 second/piece including target acquisition, alignment, and verification.
PRINT HEAD
• Convenient Access: Cylinder-driven Up/down movement of squeegee and flood-coater allows easy access for screen frame loading/unloading and ink cleaning.
• Smooth Movement: Printing head stroke is driven by Japanese DC motor with encoder along a linear guide rail for stability and accuracy throughout the print stroke.
• Wide range of adjustable parameters: Squeegee angle is adjustable, as is depth of squeegee and flood-coater.
SCREEN FRAME HOLDER
• Frame Width Detector: Screen outer width can be automatically detected, and printing stroke will be adjusted accordingly to avoid crashing into screen frame and frame holder assembly.
• Easy Adjustment: Strong, rigid screen frame holder is designed for standardized screen frame sizes. Adjustment of frame holder cantilever is easy and fast.
• Fast Loading/Unloading: Pneumatic screen clamps and 3 movable registration knobs enable fast loading and unloading of screen frame.
• Adjustable Screen Lifting: Digitally controlled servo peel-off distance of start/end point can be set relative to image size, with variable speed and height control. Touch screen setting of this print parameter can be stored, saved, and recalled for repeat jobs and/or common applications. Reduces setup and changeovers.
TOUCHSCREEN CONTROLS
• HMI Touchscreen: 5.7” + 15” color touch screen panel. Detailed function setups can be accessed, and parameters can be saved and recalled. Enables digital process management and quick job setups.
• Digital storage: Alignment data and parameter settings can be saved in flash memory of machine or any other media on network.
• Language Selection: Chinese or English interface can be selected.
• Protective Cover: Touch screen is protected by transparent cover to avoid damage.
OPTICAL ALIGNMENT SYSTEM
• Computer-controlled Optical Alignment System: Industrial computer with Windows OS drives 3-axis servo system for fast and accurate alignment.
• High Resolution CCD: High resolution CCD enables high magnification of live target for analysis and comparison.
• CCD Cameras: 4 CCD cameras 130mm above table can have positions independently adjusted by operator.
OFFLOADING
• Vacuum Pad Offloading System: Moves substrate automatically to IR dryer without marks or damage from handling.
SAFETY
• Error Message Display: Upon operation error all movement is stopped. An error message will be displayed and restart icon will appear on the touch screen.
• Emergency Stop Device: Equipped emergency stop button and safety bars immediately halt all motion when activated.
Specification | ATMAGP 50PP Metric | ATMAGP 50PP US Standard Units |
Machine dimensions (WxDxH) | 1870 x 1670 x 1660mm | 73 ⅝" x 65 ¾" x 65 ⅜" |
Machine weight | 620 kgs | 1,367 lbs |
Printing table height | 980+50 mm | 38 ⅝" + 2" |
Substrate thickness | 0.3 ~ 2.0 mm | 0.01" ~ ⅛" |
Max. printing area (DxW) | 300 x 400 mm | 11 ¾" x 15 ¾" |
Min. printing area (DxW) | 100 x 160 mm | 4" x 6 ¼" |
Max. capacity | 420 P/H | 420 P/H |
Air source pressure | 6.3 - 7.7 kg/cm² | 90 - 110psi |
Air consumption | 8 L/cycle | 0.28 cf/cycle |
Power source | 3∮,220/380V,50/60Hz | 3∮,220/380V,50/60Hz |
Power consumption | 2.3 Kw | 2.3 Kw |
Screen standby height | 20 mm | ¾" |
Screen up height | 360 mm | 14 ⅛" |
Repeat accuracy of screen up/down | 0.1 mm | 0.0394″ |
Speed of screen up/down | 1650 mm/sec | 65″/sec |
Screen lifting delay | 0 ~ 10 sec | 0 ~ 10 sec |
Standard printing speed | 55 ~ 550 mm/sec | 2 ⅛" ~ 21 ⅝" |
Max. printing stroke | 500 mm | 19 ¾" |
Parallelism of print-head guide rail and table | < 0.1 mm | < 0.0394″ |
Downward depth of squeegee | 12 mm | ½" |
Max. O/D frame size (DxW) | 700 x 900 mm | 27 ½" x 35 ⅜" |
Min. O/D frame size (DxW) | 600 x 650 mm | 23 ⅝" x 25 ⅝" |
Frame height | 20 ~ 40 mm | ¾" ~ ⅝" |
Table size (DxW) | 430 x 550 mm | 16 ⅞ x 21 ⅝" |
Vacuum area (DxW) | 5240 x 340 mm | 9 ½" x 13 ⅜" |
Shuttle table traveling distance | 640 mm | 25 ¼" |
Shuttle table speed | 1000 mm/sec | 39 ⅜"/sec |
Repeatability accuracy | 0.005 mm | 0.0002" |
CCD WD (working distance) | 150 mm | 5 ⅞" |
CCD FOV (field of view) | 11.1 x 8.3 mm | ½" x ⅜" |
CCD capture area | X= ±200 ~ ±80 mm | X= ±7 ⅞" ~ ±3 ⅛" |
Vacuum cup quantity / diameter | 4 / ø 10 mm | 4 / ø ⅜" |
SCREEN FRAME HEIGHT: For the convenience of our customers, ATMA prepares all machines sold through RH Solutions to accept roller, diamond chase, and stretch and glue frames with heights 28mm - 52mm (1.1" - 2").